Spis treści
Co to jest tabela spawania MIG/MAG?
Tabela spawania MIG/MAG to nieoceniona pomoc przy doborze optymalnych ustawień spawarki. Oferuje rekomendowane wartości kluczowych parametrów, takich jak prąd spawania i napięcie łuku, a także sugeruje prędkość podawania drutu oraz odpowiedni rodzaj gazu osłonowego. Wybór właściwych ustawień zależy od wielu istotnych czynników.
Przede wszystkim, kluczową rolę odgrywają właściwości spawanego materiału – jego rodzaj i grubość. Nie można również pominąć średnicy drutu elektrodowego oraz pozycji, w jakiej odbywa się spawanie. Korzystając z tabeli spawania MIG/MAG, zdecydowanie łatwiej jest dobrać parametry zapewniające wysoką jakość spoiny. Pozwala ona zminimalizować ryzyko potencjalnych wad spawalniczych, dostarczając informacji o optymalnym dostosowaniu prądu do używanej średnicy drutu. Dodatkowo, wskazuje, jak dopasować ilość gazu osłonowego w zależności od grubości drutu spawalniczego.
Jakie parametry spawania mają znaczenie w metodzie MIG/MAG?
W spawalnictwie metodami MIG/MAG, precyzyjna tabela parametrów spawania okazuje się nieoceniona. Zawiera ona szczegółowe wytyczne dotyczące doboru ustawień, które bezpośrednio wpływają na jakość i wytrzymałość tworzonego złącza. Taka tabela uwzględnia kilka kluczowych czynników, takich jak:
- natężenie prądu spawania, które reguluje tempo topienia się drutu, kształt spoiny oraz głębokość, na jaką następuje wtopienie w materiał – większe natężenie przyspiesza proces topienia i zapewnia głębszą penetrację, co jest szczególnie istotne przy łączeniu grubszych elementów,
- napięcie łuku spawalniczego, które determinuje stabilność łuku oraz ogólną jakość spoiny – odpowiednio dobrane napięcie pomaga uniknąć potencjalnych defektów, takich jak porowatość czy niedostateczne przetopienie,
- prędkość podawania drutu, która ma bezpośredni wpływ na stabilność łuku – zbyt wolne podawanie może skutkować niestabilnym łukiem i słabym połączeniem, podczas gdy nadmierna prędkość grozi powstawaniem odprysków i przegrzewaniem materiału,
- rodzaj oraz natężenie przepływu gazu osłonowego, które wpływają na właściwości fizyczne łuku i głębokość przetopu – wybór konkretnego gazu, takiego jak argon, hel, dwutlenek węgla lub ich mieszanki, zależy od rodzaju spawanego materiału i pożądanych cech spoiny (na przykład, argon sprawdza się doskonale przy spawaniu aluminium),
- średnica drutu elektrodowego, która determinuje gęstość prądu i w konsekwencji wpływa na głębokość wtopienia – jej dobór powinien uwzględniać grubość łączonych elementów i natężenie prądu,
- prędkość spawania, która wpływa na głębokość penetracji i szerokość tworzonej spoiny – zbyt szybkie przesuwanie elektrody może prowadzić do braku przetopu, podczas gdy zbyt wolne może skutkować przegrzewaniem i deformacją,
- długość łuku spawalniczego, która ma wpływ na stabilność całego procesu – zbyt długa odległość może powodować powstawanie odprysków, natomiast zbyt krótka – zwarcia i gaśnięcie łuku.
Jakie parametry są zawarte w tabeli spawania MIG/MAG?
Tabela parametrów spawania MIG/MAG to praktyczne narzędzie, które znacząco upraszcza proces spawania. Znajdziemy w niej kluczowe dane, takie jak:
- sugerowane natężenie prądu,
- napięcie łuku spawalniczego,
- prędkość podawania drutu.
Wszystkie te wartości są precyzyjnie dostosowane do konkretnej grubości używanego drutu elektrodowego. Co więcej, wskazówki w tabeli obejmują zalecany przepływ i typ gazu osłonowego, a ich właściwy wybór jest ściśle związany z rodzajem spawanego materiału. Na przykład, do obróbki stali węglowej stosuje się inne ustawienia niż w przypadku stali nierdzewnej lub aluminium. Nie bez znaczenia pozostaje też grubość samego materiału. Tabela parametrów uwzględnia także pozycję spawania, ponieważ spawanie w poziomie wymaga innych ustawień niż w pionie czy w pozycji sufitowej. Kolejnym aspektem jest stopień automatyzacji procesu – spawanie może być wykonywane ręcznie, w trybie półautomatycznym lub w pełni automatycznym. Właściwe dobranie wszystkich tych parametrów jest gwarancją uzyskania trwałej i estetycznej spoiny.
Jakie są kluczowe ustawienia przed rozpoczęciem spawania MIG/MAG?
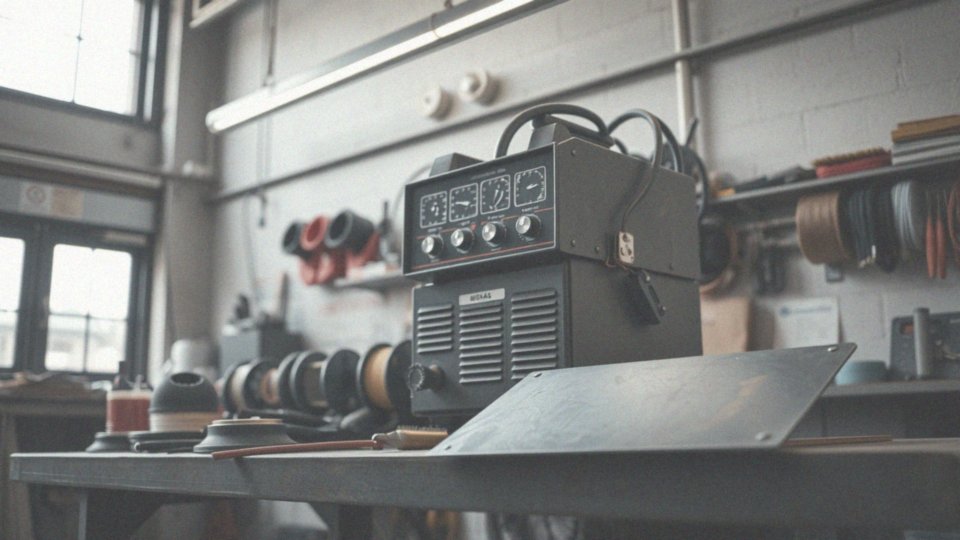
Zanim w ogóle zabierzesz się za spawanie, upewnij się, że wszystko masz idealnie dograne. To naprawdę kluczowe! Pamiętaj o następujących elementach:
- Ustaw odpowiedni prąd spawania – to on decyduje, jak będzie topił się drut i jak głęboko wniknie w materiał,
- nie zapomnij o napięciu łuku, które dba o jego stabilność, a to przekłada się na solidną spoinę,
- prędkość podawania drutu też musi być idealnie zsynchronizowana, żeby spawanie szło gładko i bez niespodzianek – zła prędkość to tylko niepotrzebne utrudnienia,
- kolejna sprawa to dobór gazu osłonowego i jego przepływ – one bezpośrednio wpływają na to, jak zachowuje się łuk spawalniczy, a odpowiedni gaz zapewni Ci pożądaną głębokość przetopu,
- pamiętaj też, żeby średnica drutu elektrodowego była dopasowana do grubości materiału, który spawasz,
- no i sprawdź biegunowość,
- upewnij się, że przewód masowy jest solidnie podpięty, najlepiej jak najbliżej miejsca, gdzie będziesz spawał,
- no i absolutna podstawa to czysta powierzchnia – usuń cały brud i zanieczyszczenia.
Tylko wtedy możesz liczyć na naprawdę mocną i trwałą spoinę.
Jakie są główne zastosowania metody MIG/MAG w przemyśle?
Metoda MIG/MAG, będąca popularną i wszechstronną techniką spawania łukowego, zyskała szerokie uznanie w rozmaitych gałęziach przemysłu. Gdzie dokładnie znajduje swoje zastosowanie?
- Produkcja konstrukcji stalowych: idealna do łączenia belek, słupów oraz ram w konstrukcjach budynków mieszkalnych, mostów czy hal produkcyjnych, gdzie kluczowa jest wytrzymałość i trwałość połączeń,
- Przemysł motoryzacyjny: spawanie karoserii aut, ram motocykli oraz elementów podwozia z dużą precyzją,
- Przemysł stoczniowy: budowa i naprawa statków, w tym spawanie kadłubów i pokładów z użyciem niezawodnych i odpornych na korozję spoin,
- Produkcja maszyn i urządzeń: od maszyn rolniczych i budowlanych po sprzęt AGD, na przykład spawanie obudowy pralki,
- Spawanie rurociągów przesyłowych: transportujących gaz, ropę naftową czy wodę, gwarantując szczelne i trwałe połączenia o wysokiej jakości,
- Robotyka spawalnicza: metoda MIG/MAG z łatwością adaptuje się do zautomatyzowanych stanowisk, zwiększając wydajność procesów produkcyjnych,
- Spawanie aluminium i metali nieżelaznych: takich jak magnez, miedź i ich stopy, z odpowiednim doborem parametrów i gazów osłonowych.
Uniwersalność metody MIG/MAG sprawia, że jest ona ceniona i niezastąpiona w wielu dziedzinach przemysłu.
Jakie są typowe aplikacje dla półautomaty spawalniczych w MIG/MAG?
Półautomaty spawalnicze MIG/MAG cieszą się ogromną popularnością i znajdują szerokie zastosowanie, zarówno w niewielkich warsztatach rzemieślniczych, jak i w rozbudowanych zakładach przemysłowych. Gdzie dokładnie możemy je spotkać?
- w warsztatach, gdzie są niezastąpione przy różnorodnych zadaniach, od drobnych napraw po bardziej wymagające projekty spawalnicze,
- w zakładach produkcyjnych, w których spawanie odgrywa kluczową rolę w procesie montażu, a półautomaty MIG/MAG doskonale się w tę rolę wpisują,
- w pracach naprawczych, umożliwiając skuteczne naprawianie uszkodzonych elementów metalowych. Dzięki nim przywracana jest pierwotna funkcjonalność konstrukcji, a nawet następuje jej wzmocnienie,
- w produkcji lekkich konstrukcji stalowych, pozwalając na tworzenie elementów wyposażenia, takich jak praktyczne regały, estetyczne balustrady, solidne ogrodzenia czy wytrzymałe ramy,
- przy spawaniu karoserii samochodowych, gdzie są wykorzystywane zarówno podczas napraw powypadkowych, jak i przy modyfikacjach, umożliwiając precyzyjne łączenie blach.
Półautomaty MIG/MAG oferują wszechstronność, umożliwiając spawanie różnych materiałów w trybie ręcznym lub półautomatycznym. Przy wyborze konkretnego modelu, kluczowym kryterium jest grubość materiałów, z którymi planujemy pracować.
Jakie wady mogą wystąpić podczas spawania MIG/MAG?
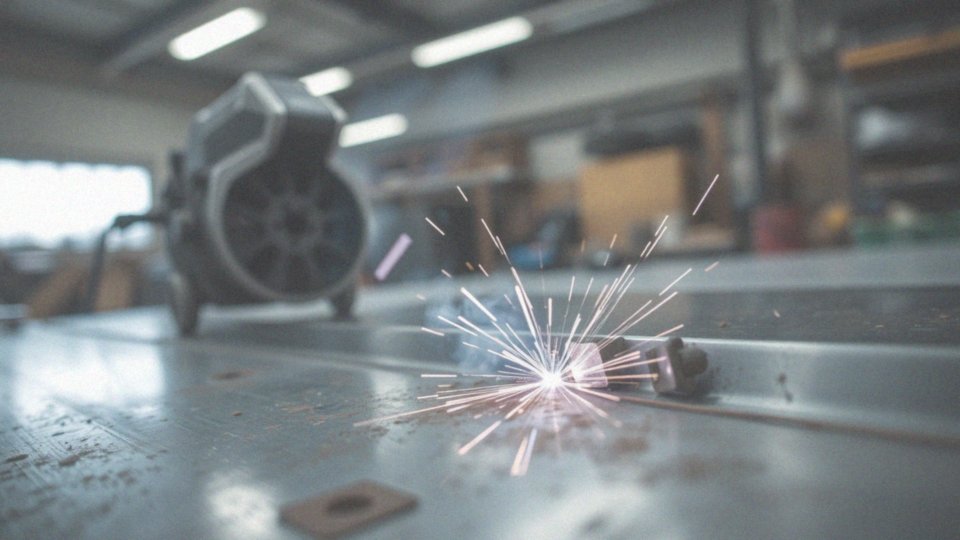
Spawanie metodą MIG/MAG, choć wszechstronne, niesie ze sobą ryzyko wystąpienia defektów, które obniżają jakość i trwałość połączenia. Wśród najczęstszych problemów spotykanych w spoinach wykonanych tą techniką, wyróżnić można:
- porowatość,
- pęknięcia,
- braki przetopu,
- podtopienia,
- wtrącenia żużla,
- deformacje.
Porowatość, czyli obecność pęcherzyków gazu uwięzionych wewnątrz spoiny, jest często skutkiem:
- nieprawidłowego doboru gazu osłonowego,
- jego niewystarczającego przepływu,
- zanieczyszczeń na powierzchni łączonych elementów,
- nadmiernej wilgotności otoczenia.
Te drobne wady osłabiają strukturę i wytrzymałość spoiny. Pęknięcia, z kolei, są efektem naprężeń powstających podczas spawania. Mogą być powodowane zarówno przez źle dobrane parametry procesu, jak i niewłaściwy skład chemiczny spawanego materiału. Rozróżnia się pęknięcia gorące, które pojawiają się w trakcie krzepnięcia spoiny, oraz pęknięcia zimne, powstające po jej ostygnięciu. Brak przetopu objawia się niedostatecznym stopieniem materiału podstawowego, co zwykle wynika ze zbyt niskiej energii spawania. Przykładowo, zbyt mały prąd lub zbyt szybkie przesuwanie spoiny może prowadzić do tego defektu. Odwrotną wadą są podtopienia, pojawiające się, gdy energia spawania jest zbyt wysoka, powodując nadmierne stopienie materiału i osłabienie krawędzi spoiny. Wtrącenia żużla to problem, który dotyka głównie spawania drutami proszkowymi. Powstający żużel, jeśli nie zostanie usunięty przed nałożeniem kolejnej warstwy, staje się integralną częścią spoiny, obniżając jej jakość. Deformacje, ostatnie z wymienionych wad, są wynikiem nierównomiernego nagrzewania i chłodzenia materiału. To prowadzi do zmian w kształcie i wymiarach elementu. Skuteczne unikanie tych problemów wymaga precyzyjnego doboru parametrów spawania, dbałości o czystość materiału bazowego, stosowania właściwego gazu osłonowego oraz odpowiedniej techniki spawania.
Jak dobrać średnicę drutu elektrodowego?
Odpowiedni dobór średnicy drutu spawalniczego ma kluczowe znaczenie dla jakości spoiny. Średnicę należy dopasować przede wszystkim do grubości spawanego materiału, ale także do natężenia prądu i pozycji spawania. Cieńsze druty, o średnicy 0,6-0,8 mm, doskonale nadają się do cienkich blach, umożliwiając precyzyjne spawanie i kontrolę nad ilością wprowadzanego ciepła – w tym przypadku warto stosować krótkie, pewne ruchy. Z kolei, przy obróbce grubszych elementów, lepiej sprawdzą się druty grubsze (1,0-1,6 mm), gwarantujące głębsze przetopienie i solidniejsze połączenie, a dodatkowo przyspieszające całą pracę. Warto pamiętać, że średnica drutu wpływa bezpośrednio na gęstość prądu i głębokość wtopienia, dlatego decyzję o jego wyborze należy podjąć w oparciu o rodzaj spoiny, którą chcemy uzyskać – spawanie pachwinowe będzie wymagało użycia innego drutu niż spawanie doczołowe.
Jak dobrać strumień gazu osłonowego do grubości materiału?
Przepływ gazu osłonowego w spawalnictwie, który mierzymy w litrach na minutę (l/min), jest zależny od kilku istotnych aspektów. W szczególności, grubość spawanego elementu ma fundamentalne znaczenie – im materiał jest masywniejszy, tym strumień gazu musi być silniejszy, aby skutecznie chronić obszar spawania.
Nie bez znaczenia pozostaje również średnica drutu elektrodowego. Przykładowo:
- spawając drutem o średnicy 0,8 mm, często wystarczający jest przepływ rzędu 8 l/min,
- gdy używamy drutu 1,0 mm, za optymalny uznaje się przepływ 10 l/min,
- w przypadku jeszcze grubszych drutów, o średnicach 1,2 mm i 1,6 mm, zapotrzebowanie to wzrasta odpowiednio do 12 l/min i 16 l/min.
Oprócz tego, na wymagany przepływ gazu wpływają również sama metoda spawania oraz warunki panujące w otoczeniu. Tam, gdzie występują przeciągi, konieczne jest zwiększenie strumienia gazu, by zagwarantować odpowiednią ochronę spoiny przed wpływem atmosfery. Niewystarczający przepływ gazu może prowadzić do powstawania porowatości i utleniania spoiny, obniżając jej wytrzymałość. Z drugiej strony, nadmierny przepływ powoduje turbulencje i zasysanie powietrza, co równie negatywnie oddziałuje na jakość. Dlatego kluczowa jest precyzyjna regulacja, którą umożliwiają reduktory gazowe, pozwalające na utrzymanie optymalnego przepływu podczas całego procesu spawania, co ma decydujące znaczenie dla uzyskania trwałej i estetycznej spoiny.
Jakie gaz osłonowy wybrać dla MIG/MAG?
Wybór odpowiedniego gazu osłonowego podczas spawania metodami MIG/MAG to kluczowa decyzja, bezpośrednio związana z rodzajem spawanego materiału. Różne gazy charakteryzują się odmiennymi właściwościami, które wpływają na stabilność łuku elektrycznego, głębokość wtopienia oraz ogólną jakość finalnej spoiny. Na przykład, do spawania popularnych stali niestopowych często wykorzystuje się prosty i ekonomiczny dwutlenek węgla (CO2). Zapewnia on dobrą penetrację spoiny. Alternatywnie, można zastosować mieszankę argonu z dwutlenkiem węgla (Ar+CO2), która oferuje bardziej stabilny łuk spawalniczy i redukuje ilość powstających odprysków w porównaniu do użycia czystego CO2. W przypadku stali nierdzewnych powszechnie stosuje się mieszanki argonu z dodatkiem tlenu (Ar+O2) lub helu (Ar+He). Tlen pełni rolę stabilizatora łuku i ułatwia proces wtopienia, natomiast hel, dzięki podwyższonej energii łuku, znajduje zastosowanie przy obróbce grubszych elementów. Do spawania aluminium, idealnym rozwiązaniem jest czysty argon (Ar) lub mieszanka argonu z helem. Argon skutecznie chroni spawany materiał przed niepożądanym utlenianiem, a hel dodatkowo poprawia charakterystykę spoiny i zwiększa głębokość wtopienia. Stosowanie właściwego gazu osłonowego ma fundamentalne znaczenie. Pozwala zminimalizować ryzyko powstawania wad spawalniczych, zapewniając spoinie optymalne właściwości mechaniczne i estetyczny wygląd.
Jak natężenie prądu spawania wpływa na jakość spoiny?
Dobór odpowiedniego prądu spawania ma zasadniczy wpływ na jakość wykonanej spoiny, oddziałując na kluczowe aspekty całego procesu. Przede wszystkim, to on decyduje o wytrzymałości i minimalizacji defektów. Przede wszystkim, zbyt wysoki prąd zwiększa głębokość wtopienia, co przekłada się na solidniejsze połączenie. Z drugiej strony, zbyt słaby prąd może uniemożliwić pełen przetop i osłabić spoinę. Prąd spawania determinuje również szerokość lica spoiny – generalnie, wyższe wartości oznaczają szersze lico. Należy jednak uważać, ponieważ zbyt duży prąd generuje nadmierne ciepło, które może spowodować deformację spawanego materiału. Niewłaściwe ustawienie prądu zwiększa ryzyko wystąpienia wad spawalniczych, takich jak podcięcia czy nadmierny rozprysk. Dobierając optymalne parametry, można znacznie zredukować to ryzyko. Warto również pamiętać, że wyższy prąd przyspiesza stapianie drutu elektrodowego, co bezpośrednio przekłada się na tempo spawania. Innymi słowy, praca staje się szybsza i bardziej efektywna.
Jakie znaczenie ma biegunowość i rodzaj prądu w procesie spawania?
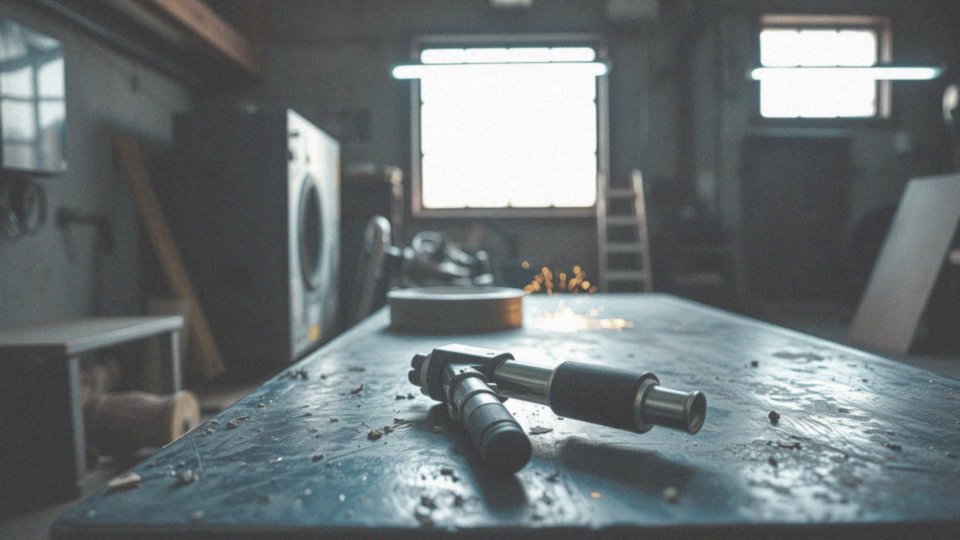
W spawaniu metodą MIG/MAG, wybór odpowiedniej biegunowości i rodzaju prądu ma fundamentalne znaczenie dla uzyskania trwałej i estetycznej spoiny. Najczęściej stosuje się prąd stały (DC), który zapewnia większą kontrolę nad procesem. Chociaż prąd przemienny (AC) również znajduje swoje zastosowanie, jest on używany zdecydowanie rzadziej.
W przypadku prądu stałego (DC), istotna jest biegunowość, która decyduje o rozkładzie ciepła między elektrodą a spawanym elementem. Najbardziej rozpowszechniona jest biegunowość dodatnia (elektroda podłączona do „+”, materiał do „-„). Ta konfiguracja sprzyja głębszemu wtopieniu i bardziej stabilnemu łukowi spawalniczemu. Z kolei biegunowość ujemna (elektroda „-„, materiał „+”) generuje mniej ciepła na elektrodzie, co skutkuje płytszym wtopieniem.
Rodzaj prądu bezpośrednio wpływa na stabilność łuku i charakterystykę spoiny. Prąd stały (DC) zapewnia stabilny łuk, precyzję i lepszą kontrolę, co jest nieocenione podczas spawania cienkich blach czy też w trudno dostępnych miejscach. Natomiast prąd przemienny (AC) przydaje się np. przy spawaniu aluminium, ponieważ efektywnie usuwa tlenki z jego powierzchni, przygotowując go do połączenia.
Podsumowując, dobór odpowiedniego prądu zależy od:
- rodzaju spawanego materiału,
- jego grubości,
- oczekiwanej jakości połączenia.
Jak prędkość spawania jest powiązana z natężeniem prądu i napięciem?
Prędkość spawania ma fundamentalne znaczenie, ponieważ bezpośrednio wpływa na ilość ciepła wprowadzanego do spawanego elementu. Spawanie zbyt wolne, przy określonym prądzie i napięciu, prowadzi do niepożądanego przegrzania, które z kolei może skutkować:
- przepaleniami,
- nadmiernym wtopieniem,
- w efekcie – defektami spoiny.
Z drugiej strony, zbyt pośpieszne łączenie materiałów grozi brakiem odpowiedniego przetopu i uzyskaniem słabego, nietrwałego połączenia. Dlatego kluczowe jest precyzyjne dopasowanie tempa pracy do parametrów prądu i napięcia. Tylko optymalna synchronizacja tych czynników gwarantuje właściwe wtopienie i pożądany kształt spoiny, minimalizując jednocześnie ryzyko wystąpienia jakichkolwiek niedoskonałości. Odpowiednia prędkość to pewność uzyskania właściwej głębokości wtopienia, co bezpośrednio przekłada się na solidność i trwałość połączenia. Krótko mówiąc, utrzymanie kontroli nad tempem pracy to podstawa udanego procesu spawania.
Jak gęstość prądu wpływa na spawanie?
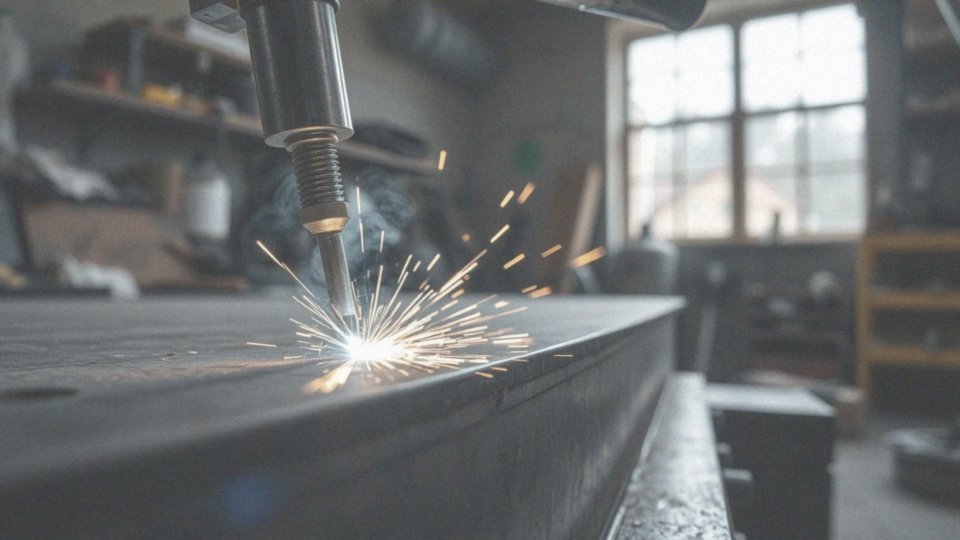
Gęstość prądu, kluczowy parametr w spawaniu MIG/MAG, definiowana jest jako stosunek natężenia prądu do przekroju drutu i ma fundamentalny wpływ na cały proces. Przede wszystkim, determinuje ona temperaturę łuku spawalniczego, a co za tym idzie, głębokość wtopienia i szybkość topienia drutu. Większa gęstość prądu to wyższa temperatura łuku, co z kolei przyspiesza topienie materiału. Odpowiednio dobrana, zapewnia solidne wtopienie, bezpośrednio wpływając na wytrzymałość wykonanej spoiny. Zbyt niska gęstość z kolei prowadzi do niestabilnego łuku i słabego wtopienia. Przeciwnie, nadmierna gęstość prądu grozi przegrzaniem drutu, powodując nadmierne rozpryski i niepożądane podcięcia w spoinach. Właściwy dobór tego parametru jest więc niezbędny, a ściśle powiązany ze średnicą używanego drutu. Dobierając średnicę, musimy uwzględnić grubość spawanego materiału oraz wymagane parametry gotowej spoiny dopasowując ją do konkretnego zadania.
Jak napięcie łuku spawalniczego wpływa na wyniki spawania?
Napięcie łuku elektrycznego w znaczący sposób determinuje jego szerokość oraz finalny wygląd spoiny, co bezpośrednio rzutuje na jakość całego procesu spawania. Utrzymanie stabilnego łuku jest możliwe dzięki dobraniu optymalnego napięcia. Ponadto, reguluje ono ilość ciepła oddawanego do spawanego elementu. Nieodpowiednie ustawienia napięcia mogą jednak generować komplikacje. Zbyt niskie napięcie skutkuje:
- zwarciami,
- destabilizacją łuku,
- niedostatecznym przetopieniem,
- osłabieniem połączenia.
Z drugiej strony, nadmiernie wysokie napięcie podnosi prawdopodobieństwo powstawania:
- odprysków,
- ryzyko wystąpienia podtopień, co negatywnie odbija się na jakości samej spoiny.
Istotnym jest, że wartość napięcia łuku jest zależna od zastosowanego gazu osłonowego.
Jaką rolę odgrywa prędkość podawania drutu elektrodowego?
Prędkość podawania drutu jest kluczowa dla prawidłowego spawania, ponieważ bezpośrednio wpływa na stabilność łuku elektrycznego, co z kolei determinuje jakość i estetykę spoiny. Kontroluje ona ilość materiału dodawanego do jeziorka spawalniczego w danym momencie, a jej nieodpowiednie ustawienie może prowadzić do poważnych problemów.
Zbyt wolne podawanie drutu destabilizuje łuk i skutkuje niedostatecznym wypełnieniem spoiny, co obniża jej wytrzymałość. Natomiast nadmierna prędkość podawania może powodować zwarcia, nadmierny rozprysk i ogólne pogorszenie jakości połączenia. Wpływa to również negatywnie na proces stapiania drutu i ostateczny kształt spoiny.
Reasumując, precyzyjne ustawienie prędkości podawania drutu to fundament udanego spawania.
Jak kąt pochylenia drutu elektrodowego wpływa na głębokość wtopienia?
Kąt nachylenia elektrody w procesie spawania MIG/MAG znacząco wpływa na finalny wygląd spoiny oraz głębokość jej wnikania w materiał. Zmiana kąta powoduje modyfikacje w działaniu sił łuku elektrycznego oraz w rozkładzie ciepła w obrębie spawanego elementu.
Spawanie z elektrodą skierowaną do przodu skutkuje płytszym wtopieniem, ale jednocześnie tworzy szerszą spoinę. Z tego względu, technika ta idealnie sprawdza się przy łączeniu cienkich arkuszy blachy. Natomiast, gdy elektroda jest pochylona do tyłu, uzyskujemy głębsze wtopienie i węższą spoinę, co jest bardziej korzystne przy spawaniu grubszych materiałów.
Odpowiedni dobór kąta nachylenia drutu spawalniczego jest kluczowy dla uzyskania spoiny o pożądanych parametrach i zapewnienia jej wysokiej jakości. Umiejętne manipulowanie tym parametrem pozwala na precyzyjne dostosowanie charakterystyki spoiny do konkretnych wymagań danego projektu.
Jak stabilność łuku spawalniczego wpływa na jakość spoin?
Stabilny łuk spawalniczy to fundament trwałej i estetycznej spoiny, mający bezpośredni wpływ na jej wytrzymałość. Gwarantuje on jednolite wtopienie metalu, co jest kluczowe dla mocnego i spójnego połączenia. Z drugiej strony, niestabilny łuk to poważny problem, ponieważ prowadzi do nierównomiernego wtopienia i szeregu wad, takich jak porowatość, braki przetopu czy podcięcia.
Stabilny łuk spawalniczy, zapewniając równomierne wtopienie, przekłada się na spoinę niezwykle trwałą i jednolitą, o jednorodnym kształcie, który łączy w sobie estetykę i funkcjonalność. Kluczowa jest także minimalizacja wad spawalniczych, ponieważ ogranicza ryzyko osłabienia konstrukcji. Co więcej, spawacz zyskuje pełną kontrolę nad procesem, co pozwala mu precyzyjnie sterować parametrami spawania.
Stabilność łuku zależy od wielu czynników. Niezwykle ważne są:
- odpowiednio dobrane parametry spawania, takie jak prąd, napięcie i prędkość podawania drutu,
- czystość gazu osłonowego, gdyż zanieczyszczenia mogą zakłócać jego stabilność,
- jakość drutu elektrodowego – wszelkie zanieczyszczenia lub wady wpływają negatywnie na proces spawania,
- umiejętności i doświadczenie spawacza, które odgrywają kluczową rolę w utrzymaniu stabilnego łuku.
Podsumowując, dążenie do stabilnego łuku jest koniecznością, aby uzyskać spoinę, charakteryzującą się nie tylko wysoką jakością, ale także spełniającą wszelkie normy wytrzymałościowe i estetyczne.
Jakie różnice występują między gazami aktywnymi a obojętnymi w spawaniu?
Podstawowa różnica między gazami aktywnymi a obojętnymi w procesach spawalniczych leży w ich interakcji z materiałem. Gazy obojętne, do których zaliczamy argon i hel, działają jako tarcza ochronna, izolując obszar spawania od otoczenia. Nie wchodzą w żadne reakcje chemiczne z samym metalem, a jedynie chronią go przed utlenianiem i zanieczyszczeniami z atmosfery. Dlatego też doskonale sprawdzają się przy obróbce metali nieżelaznych, takich jak aluminium, magnez czy tytan, które często spawa się właśnie w ich osłonie.
Z kolei gazy aktywne, np. dwutlenek węgla (CO2) lub mieszanki argonu z CO2, włączają się aktywnie w sam proces spawania. Uczestniczą one w reakcjach zachodzących w łuku spawalniczym, wpływając bezpośrednio na jego charakterystykę. W ten sposób modulują one zarówno kształt powstałej spoiny, jak i jej właściwości mechaniczne. Z tego powodu najczęściej wykorzystuje się je do spawania stali niestopowych oraz niskowęglowych.
Dobór właściwego gazu jest uzależniony przede wszystkim od rodzaju spawanego materiału oraz od oczekiwanej jakości połączenia. Gazy obojętne są niezastąpione, gdy kluczowa jest ochrona przed niepożądanymi reakcjami chemicznymi. Natomiast gazy aktywne znajdują zastosowanie tam, gdzie istotna jest kontrola parametrów łuku i właściwości samej spoiny. Zatem, prawidłowy wybór gazu spawalniczego ma decydujący wpływ na osiągnięcie optymalnych rezultatów.