Spis treści
Jak ustawić migomat do spawania cienkiej blachy?
Aby skutecznie spawać cienkie blachy migomatem, trzeba uwzględnić kilka kluczowych aspektów. Przede wszystkim, należy właściwie dobrać parametry spawania, a więc napięcie łuku oraz natężenie prądu. Równie istotna jest prędkość podawania drutu, którą należy precyzyjnie dostosować. Kolejna sprawa to odpowiednia elektroda – musi być ona kompatybilna zarówno z grubością blachy, jak i rodzajem spawanego metalu. Dla przykładu, do spawania stali użyjemy innej elektrody niż w przypadku aluminium. Nie można zapominać o gazie osłonowym. Argon lub mieszanka argonu z dwutlenkiem węgla (CO₂) zabezpieczą spoinę przed utlenianiem. Drobne szczegóły, takie jak długość wystającego drutu i kąt nachylenia uchwytu spawalniczego, również mają wpływ na jakość spawu. To one decydują o stabilności łuku i minimalizują powstawanie odprysków. Precyzyjna regulacja indukcyjności oraz funkcje Arc Force i Hot Start mogą znacząco poprawić estetykę Twoich spoin. W doborze optymalnych ustawień pomogą Ci arkusze testowe lub specjalne aplikacje. Warto też poszukać rekomendacji doświadczonych spawaczy, którzy pracowali w podobnych warunkach. I pamiętaj – wprawa czyni mistrza, więc nie zrażaj się początkowymi trudnościami!
Jakie są wymagania dotyczące ustawienia migomatu dla spawania cienkiej blachy?
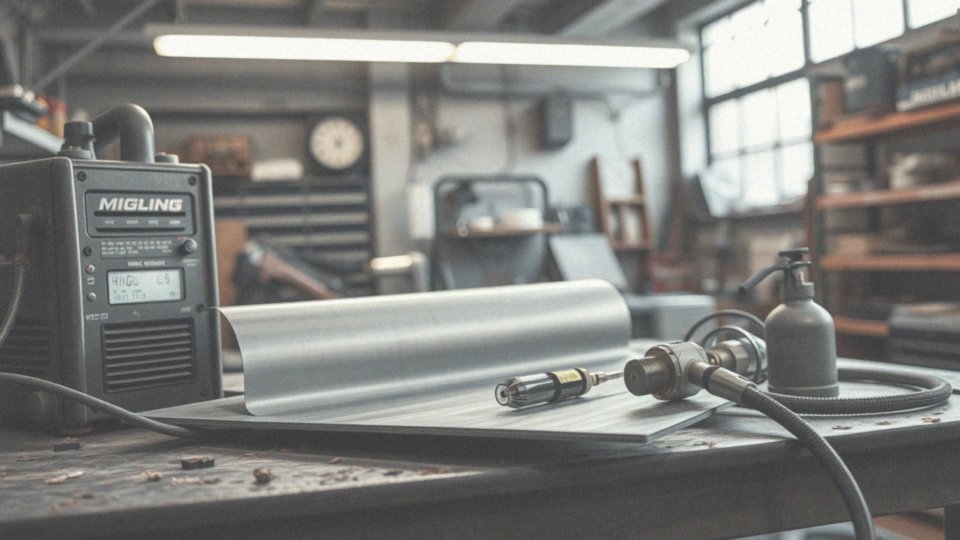
Spawanie cienkiej blachy migomatem wymaga pewnej wprawy, aby uniknąć typowych problemów, takich jak przepalenia czy deformacje. Jak zatem podejść do tego zadania? Najważniejsze są właściwe parametry spawania. Należy precyzyjnie dobrać prąd, napięcie oraz tempo podawania drutu. Z reguły, cienki drut spawalniczy, o średnicy 0,6-0,8 mm, sprawdza się najlepiej. Nie można zapomnieć o odpowiednim gazie osłonowym. Czysty argon lub jego mieszanka z CO₂ efektywnie zabezpieczają spoinę przed dostępem powietrza i zanieczyszczeniami. Przepływ gazu dostosowujemy do średnicy drutu, najczęściej w zakresie 8-12 litrów na minutę. Skrupulatna regulacja podajnika drutu i reduktorów gazu zapewni stabilny proces spawania i zminimalizuje powstawanie odprysków. Niezwykle istotne jest również odpowiednie oczyszczenie powierzchni spawanej blachy. Schludna i odtłuszczona blacha to fundament trwałej spoiny!
Dlaczego staranne przygotowanie powierzchni jest kluczowe przed spawaniem?
Odpowiednie przygotowanie powierzchni przed spawaniem cienkich blach to podstawa sukcesu. Gwarantuje ono solidne i trwałe połączenie. Dlatego tak ważne jest usunięcie wszelkich zanieczyszczeń, takich jak:
- rdza,
- oleje,
- smary,
- pozostałości farb,
- tlenki, które negatywnie wpływają na proces spawania.
Ich obecność może prowadzić do porowatości spoiny, a w konsekwencji, do osłabienia całej konstrukcji. Skrupulatne oczyszczenie powierzchni znacząco poprawia przyleganie spoiwa, co przekłada się na estetyczny wygląd i większą wytrzymałość złącza. Czysta powierzchnia minimalizuje ryzyko problemów podczas spawania i zapewnia stabilny łuk elektryczny. Ma to szczególne znaczenie w przypadku cienkich blach, gdzie precyzja odgrywa zasadniczą rolę.
Jakie parametry spawania należy dostosować do materiału?
Dobór odpowiednich parametrów spawania ma kluczowe znaczenie dla jakości połączenia i bezpośrednio wpływa na jego trwałość oraz wygląd. Są one bowiem ściśle powiązane z właściwościami spawanego materiału. Wśród najważniejszych czynników, które należy wziąć pod uwagę, znajdują się:
- natężenie prądu,
- napięcie łuku,
- prędkość podawania drutu spawalniczego,
- rodzaj użytego gazu osłonowego,
- średnica drutu – te elementy również mają ogromny wpływ na proces.
Ustawienia spawarki dostosowuje się indywidualnie do każdego spawanego materiału. Przykładowo, parametry spawania stali konstrukcyjnej będą zupełnie inne niż te stosowane do stali nierdzewnej. Podobnie, specyfika aluminium, miedzi i ich stopów wymaga odmiennych ustawień. Chociażby spawanie aluminium charakteryzuje się wykorzystaniem argonu jako gazu osłonowego i dedykowanego drutu aluminiowego. Właśnie dlatego precyzyjny dobór parametrów jest absolutnie nieodzowny, jeśli zależy nam na solidnym i estetycznym efekcie końcowym.
Jak dobierać natężenie prądu do grubości blachy?
Jak precyzyjnie dobrać natężenie prądu podczas spawania cienkich blach, aby uzyskać trwałe i estetyczne połączenie? To kluczowa kwestia! Zbyt wysoka wartość prądu grozi przepaleniem delikatnego materiału, natomiast zbyt niska skutkuje słabą i nietrwałą spoiną. Uniwersalna reguła nie istnieje, jednak warto kierować się pewnymi wytycznymi.
W przypadku zwykłej stali sprawdzi się zasada 30-40 amperów na każdy milimetr grubości blachy – to dobry punkt odniesienia. Jeżeli pracujesz z ultracienkimi blachami (poniżej 1 mm), zacznij od niższego natężenia i stopniowo je zwiększaj, uważnie obserwując reakcję materiału. Kluczem jest znalezienie takiego prądu, który zapewni stabilny łuk spawalniczy. Jeziorko spawalnicze powinno charakteryzować się odpowiednią wielkością i płynnością. Pamiętaj o rodzaju spawanego materiału! Regulacja parametrów dla aluminium będzie inna niż dla stali. Doświadczenie odgrywa tu zasadniczą rolę. Przeprowadzaj próby na niewielkich fragmentach materiału – to najlepszy sposób na dobranie optymalnego prądu do konkretnej grubości i gatunku blachy. Pomocne mogą być również tabele spawalnicze oraz specjalistyczne aplikacje, które sugerują wstępne ustawienia.
Jak ustawić prędkość podawania drutu dla cienkiej blachy?
Odpowiednie ustawienie prędkości podawania drutu to podstawa, jeśli zależy nam na solidnej spoinie. Zwłaszcza przy obróbce delikatnych blach, precyzja ma ogromne znaczenie. Staramy się osiągnąć perfekcyjne dopasowanie tej prędkości do natężenia prądu, co zapewnia stabilny łuk spawalniczy i pozwala uniknąć problemów takich jak:
- niestabilność łuku spawalniczego,
- przerywana spoina,
- nadmierne odpryski,
- przepalenia.
Warto pamiętać, że do cienkich blach zwykle stosuje się mniejszą prędkość podawania drutu niż w przypadku grubszych materiałów. Kluczem do sukcesu jest uważna obserwacja jeziorka spawalniczego i szybkie reagowanie na wszelkie zmiany – to gwarantuje najlepsze rezultaty. Spawarki MIG/MAG często oferują regulację indukcyjności, co stanowi dodatkowy atut, stabilizując cały proces spawania. Ponadto, aplikacje i tabele z ustawieniami spawania mogą okazać się nieocenioną pomocą. Zawierają one sugestie dotyczące prędkości podawania drutu, dostosowane do grubości blachy i rodzaju spawanego materiału, czyniąc pracę łatwiejszą i bardziej efektywną.
Jak wybrać odpowiednią elektrodę do spawania cienkiej blachy?
Wybór właściwej elektrody spawalniczej to klucz do uzyskania solidnych i estetycznych spoin. Aby osiągnąć optymalne rezultaty, należy wziąć pod uwagę kilka istotnych kwestii. Przede wszystkim, kluczowe jest dopasowanie średnicy drutu do grubości łączonych elementów. Zasada jest prosta: im cieńszy materiał, tym cieńsza elektroda. Dla przykładu, do spawania cienkich blach idealnie sprawdzą się druty o średnicy 0,6-0,8 mm.
Równie ważny jest rodzaj elektrody, który powinien być kompatybilny z materiałem bazowym. I tak:
- do stali niskowęglowej polecane są druty SG2 lub SG3, gwarantujące trwałe połączenie,
- w przypadku aluminium, konieczne jest zastosowanie drutów aluminiowych, takich jak AlMg5 lub AlSi5, przy czym konkretny wybór zależy od składu stopu,
- a do stali nierdzewnej dedykowane są elektrody nierdzewne, np. 308LSi lub 316LSi.
Nie można pominąć roli odpowiedniego gazu osłonowego, który pełni funkcję ochronną, zabezpieczając spoinę przed wpływem atmosfery i zanieczyszczeniami. Dobrze dobrana elektroda to gwarancja stabilnego łuku elektrycznego podczas spawania, minimalizacja odprysków oraz zapewnienie właściwego przetopu. Z kolei, użycie niewłaściwej elektrody może prowadzić do szeregu komplikacji, takich jak niestabilny łuk, nadmierna ilość odprysków, porowatość spoiny lub jej obniżona wytrzymałość. Dlatego warto poświęcić czas na dokładne zapoznanie się z zaleceniami producentów materiałów spawalniczych i wybrać elektrodę optymalnie dopasowaną do danego zadania.
W jaki sposób gaz ochronny wpływa na jakość spoiny?
Gaz osłonowy odgrywa kluczową rolę w procesie spawania, zwłaszcza przy cienkich blachach, bezpośrednio wpływając na trwałość i jakość wykonanej spoiny. Jego podstawowym zadaniem jest zabezpieczenie jeziorka spawalniczego oraz roztopionego metalu przed negatywnym wpływem czynników atmosferycznych, takich jak tlen, azot i wilgoć. Te zanieczyszczenia mogą wchodzić w reakcje z metalem, prowadząc do powstawania porowatości, wtrąceń oraz osłabienia struktury spoiny. Dobór odpowiedniego gazu osłonowego ma znaczący wpływ na stabilność łuku spawalniczego, głębokość wtopienia, ilość powstających odprysków oraz ogólną jakość połączenia.
Jakie gazy znajdują najczęstsze zastosowanie?
- Argon (Ar): jest to gaz szczególnie polecany do spawania aluminium, stali nierdzewnej oraz innych metali nieżelaznych. Zapewnia on stabilny łuk i pozwala uzyskać czystą spoinę przy minimalnym ryzyku wystąpienia wad,
- Dwutlenek węgla (CO₂): charakteryzuje się niską ceną i sprawdza się w spawaniu stali węglowych. Zapewnia dobre wtopienie, choć generuje więcej odprysków w porównaniu do argonu,
- Mieszanki argonu i CO₂: stanowią popularne rozwiązanie przy spawaniu stali węglowych i niskostopowych. Umożliwiają znalezienie kompromisu między kosztem, jakością spoiny i ilością powstających odprysków. Przykładowo, mieszanka zawierająca 82% argonu i 18% CO₂ jest uważana za bardzo uniwersalną,
- Mieszanki argonu z tlenem (O₂): dodatek niewielkiej ilości tlenu (zazwyczaj od 1 do 5%) do argonu poprawia stabilność łuku, co ułatwia spawanie stali nierdzewnych,
- Hel (He): stosowany jest do spawania metali wymagających intensywnego dopływu ciepła, takich jak miedź czy niektóre stopy aluminium. Zapewnia on głębokie wtopienie i wysoką jakość spoiny.
Należy pamiętać, że przepływ gazu osłonowego powinien być dostosowany do rodzaju spawanego materiału, grubości drutu oraz warunków otoczenia. Zbyt mały przepływ nie zapewni odpowiedniej ochrony, natomiast zbyt duży może powodować turbulencje i zasysanie powietrza do jeziorka spawalniczego. Optymalny przepływ zazwyczaj mieści się w zakresie od 8 do 12 litrów na minutę, a reduktor z rotametrem pozwala na precyzyjne ustawienie wymaganej wartości.
Niewłaściwy dobór gazu osłonowego lub nieodpowiedni przepływ mogą prowadzić do poważnych problemów podczas spawania, takich jak powstawanie porów, pęknięć, wtrąceń i osłabienie spoiny. Dlatego przed rozpoczęciem spawania należy dokładnie zapoznać się z zaleceniami producenta materiałów spawalniczych i odpowiednio dostosować parametry spawania do konkretnego zadania.
Jakie jest znaczenie napięcia łuku spawalniczego dla spoiny?
Napięcie łuku elektrycznego w procesie spawania MIG/MAG odgrywa zasadniczą rolę w osiągnięciu wysokiej jakości połączenia. Decyduje ono o stabilności łuku, geometrii spoiny oraz minimalizacji odprysków. Dobrze dobrane napięcie gwarantuje jednolite wtopienie materiału i pożądany profil spoiny. Zbyt niskie napięcie może skutkować niestabilnym łukiem i zwarciami, co z kolei prowadzi do zwiększonej produkcji odprysków. Przeciwnie, nadmierne napięcie niesie ryzyko przegrzania obrabianego elementu i powstawania podtopień.
Ustalenie idealnego napięcia jest uzależnione od kilku czynników. Kluczowe znaczenie ma:
- rodzaj spawanego metalu – czy to stal węglowa, nierdzewna, czy aluminium,
- grubość łączonych elementów,
- rodzaj gazu osłonowego, na przykład argon, dwutlenek węgla lub ich mieszanki,
- średnica wykorzystywanego drutu elektrodowego.
Napięcie ma bezpośredni wpływ na transfer metalu. Wyższe wartości sprzyjają łukowi natryskowemu, w którym stopiony metal przenoszony jest w formie drobnych kropel. Niższe napięcia z kolei skutkują powstawaniem łuku zwarciowego lub przejściowego, gdzie krople są większe i mogą generować rozpryski. Z tego powodu dokładna regulacja napięcia jest niezbędna do uzyskania trwałej i estetycznej spoiny.
Wiele nowoczesnych spawarek MIG/MAG posiada funkcje synergiczne, które automatycznie dopasowują napięcie do innych nastawów, takich jak prąd spawania i prędkość podawania drutu, co znacznie upraszcza proces optymalizacji parametrów spawania.
Jak zminimalizować ryzyko przegrzania blachy podczas spawania?
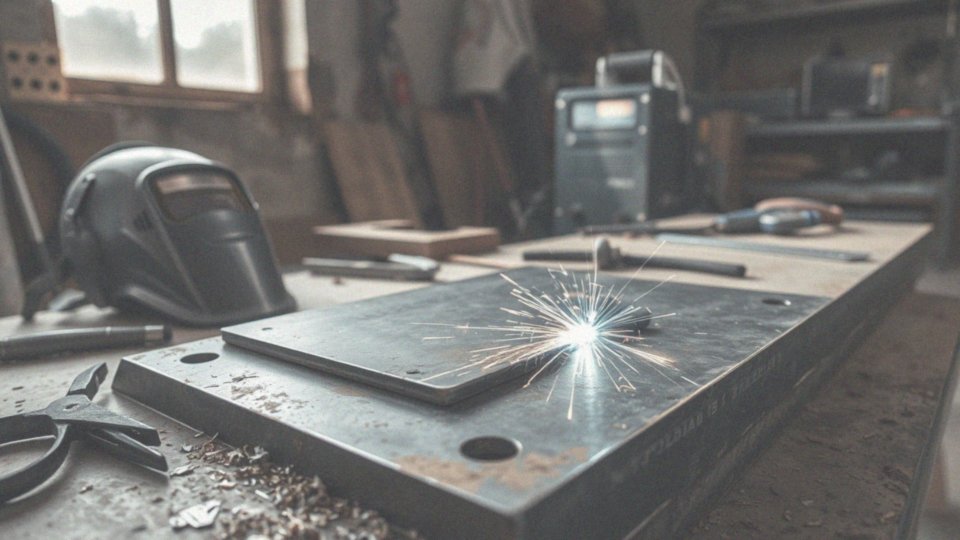
Aby uniknąć problemów z przegrzewaniem cienkiej blachy podczas spawania, kluczowa jest precyzyjna kontrola ciepła. Należy wziąć pod uwagę następujące aspekty:
- odpowiednie dopasowanie natężenia prądu do grubości materiału – zbyt wysoki prąd niemal zawsze skutkuje przepaleniem,
- istotna jest prędkość spawania – zbyt powolne tempo pracy powoduje kumulację ciepła w jednym obszarze, co może prowadzić do deformacji elementu,
- spawanie impulsowe oferuje znakomitą kontrolę nad ciepłem, znacząco redukując ryzyko przegrzania – warto rozważyć tę metodę,
- chłodzenie spawanego elementu pomiędzy kolejnymi etapami pomaga utrzymać optymalną temperaturę i zapobiega nadmiernemu nagrzewaniu,
- wybór właściwego gazu osłonowego, takiego jak argon lub mieszanka argonu z CO₂, stabilizuje łuk spawalniczy i ogranicza ilość ciepła przekazywanego do materiału,
- techniki takie jak spawanie z przerwami dają czas na odprowadzenie ciepła, minimalizując ryzyko deformacji,
- regulacja indukcyjności spawarki ma wpływ na charakterystykę łuku i pomaga unikać przegrzewania – dostosuj indukcyjność do grubości blachy i innych parametrów spawania, aby uzyskać najlepsze rezultaty.
Jakie techniki zapewniają precyzyjne spawanie cienkich blach?
Spawanie cienkich blach wymaga specyficznego podejścia, aby uniknąć niepożądanych odkształceń czy przepaleń. Istnieje kilka sprawdzonych metod, które warto mieć w zanadrzu:
- stosuj krótkie odcinki spoin. Przerywane spawanie minimalizuje ilość ciepła wprowadzanego do materiału, co skutecznie zapobiega jego deformacji,
- pomyśl o chłodzeniu. Możesz chłodzić spawany obszar strumieniem powietrza lub gazu osłonowego, co przyspieszy odprowadzanie ciepła i pomoże utrzymać niższą temperaturę,
- używaj podkładek chłodzących. Umieszczone pod spawanym złączem podkładki, wykonane np. z miedzi lub aluminium, jeszcze efektywniej odprowadzają ciepło i dodatkowo zabezpieczają przed przepaleniem,
- rozważ spawanie impulsowe, które daje znakomitą kontrolę nad ciepłem wprowadzanym do materiału dzięki precyzyjnej modulacji prądu spawania,
- zwróć uwagę na prawidłową pozycję uchwytu spawalniczego. Utrzymuj dyszę w stałej odległości od blachy (zwykle 5-10 mm) i pod odpowiednim kątem pochylenia (ok. 70-80 stopni w kierunku spawania). Równomierne prowadzenie uchwytu to podstawa dla stabilnego łuku i uzyskania spoiny wysokiej jakości,
- warto zainwestować w spawarkę MIG/MAG z regulacją, oferującą precyzyjne ustawienia parametrów takich jak Arc Force i Hot Start. Funkcje te ułatwiają rozpoczęcie spawania i stabilizują cały proces, co przekłada się na mniejsze ryzyko powstawania defektów,
- użyj odpowiedniego drutu elektrodowego. Cieńszy drut (np. 0,6-0,8 mm) zapewni Ci większą precyzję podczas pracy z cienkimi blachami,
- pamiętaj, iż czystość materiału oraz jego staranne przygotowanie mają niebagatelny wpływ na precyzję i trwałość spoiny. Zadbaj o to, a efekt Cię zadowoli!