Spis treści
Jaki gaz do spawania migomatem wybrać?
Wybór właściwego gazu osłonowego do spawarki MIG/MAG to sprawa fundamentalna, a jego dobór powinien być podyktowany przede wszystkim rodzajem spawanego materiału. Przykładowo, do aluminium idealny będzie czysty argon, który zapewnia skuteczną ochronę przed utlenianiem w trakcie spawania. Natomiast do stali węglowych i niskostopowych powszechnie stosuje się mieszanki argonu z dwutlenkiem węgla (Ar/CO2), których proporcje można dopasować do konkretnych potrzeb.
Odpowiedni dobór gazu osłonowego ma niebagatelny wpływ na cały proces spawania. Wpływa on nie tylko na stabilność łuku, co jest niezwykle istotne, ale również determinuje jakość finalnej spoiny: jej wytrzymałość, estetykę i głębokość wtopienia. Dodatkowo, ma on znaczenie dla komfortu pracy spawacza, minimalizując powstawanie odprysków i dymu.
W metodzie MIG (Metal Inert Gas) wykorzystuje się gazy obojętne, takie jak argon, hel, lub ich mieszanki. Charakteryzują się one tym, że nie wchodzą w reakcje chemiczne ze spawanym materiałem. Z kolei w metodzie MAG (Metal Active Gas) stosuje się gazy aktywne, w szczególności dwutlenek węgla (CO2) lub mieszanki z jego udziałem, które aktywnie oddziałują na proces spawania.
Jakie są rodzaje gazów spawalniczych?
Gazy wykorzystywane w spawalnictwie dzielimy zasadniczo na dwie grupy: osłonowe i palne. Te pierwsze, gazy osłonowe, odgrywają fundamentalną rolę w metodach MIG/MAG i TIG, zabezpieczając jeziorko spawalnicze przed szkodliwym działaniem atmosfery. W tej grupie wyróżniamy:
- gazy obojętne (zwane też inertnymi), takie jak argon i hel,
- gazy aktywne, do których zaliczamy dwutlenek węgla i mieszanki z dodatkiem tlenu.
Gazy obojętne pełnią funkcję czysto ochronną – nie wchodzą w reakcje chemiczne ze stopionym metalem, dzięki czemu chronią spoinę przed zanieczyszczeniami. Popularność argonu wynika z jego dostępności i wszechstronności, natomiast hel, mimo wyższej ceny, gwarantuje efektywniejsze wnikanie ciepła. Z kolei gazy aktywne wchodzą w interakcje ze spawanym materiałem, wpływając na stabilność łuku elektrycznego i kształt samej spoiny. Niewielki dodatek tlenu do mieszanki gazowej potrafi podnieść temperaturę łuku i poprawić zwilżalność spoiny. Gazy palne, takie jak acetylen i propan, znajdują zastosowanie przede wszystkim w procesach cięcia i lutowania. Acetylen, dzięki bardzo wysokiej temperaturze płomienia, jest szczególnie skuteczny przy cięciu grubych elementów, podczas gdy propan, jako rozwiązanie ekonomiczniejsze, sprawdza się w mniej wymagających pracach. Niezwykle istotna jest czystość gazu spawalniczego. Jakiekolwiek zanieczyszczenia mogą prowadzić do powstawania porowatości w spoinie, osłabienia jej wytrzymałości oraz innych problemów. Dlatego wybór gazów o wysokim stopniu czystości jest gwarancją najlepszych i najbardziej trwałych rezultatów.
Jakie gazy osłonowe są najczęściej używane w spawaniu?
Najpopularniejsze gazy wykorzystywane w spawalnictwie to przede wszystkim argon (Ar) i dwutlenek węgla (CO2), a także ich mieszanki, zwłaszcza te o proporcji Ar/CO2. Popularność argonu wynika z jego wszechstronności. Pozwala on na spawanie zarówno delikatnego aluminium, jak i wytrzymałej stali nierdzewnej, a dodatkowo gwarantuje stabilny łuk elektryczny, co przekłada się na czystą i estetyczną spoinę.
Z drugiej strony, dwutlenek węgla stanowi ekonomiczniejszą alternatywę, idealną do obróbki stali węglowych i niskostopowych. Należy jednak pamiętać, że jego użycie wiąże się z powstawaniem większej ilości odprysków. Mieszanki argonu z dwutlenkiem węgla to rozwiązanie kompromisowe, łączące zalety obu gazów. Zapewniają one stabilny łuk spawalniczy i wysoką jakość łączenia, znajdując szerokie zastosowanie w różnych typach prac spawalniczych.
Jakie są właściwości gazu osłonowego?
Wybór odpowiedniego gazu osłonowego to klucz do uzyskania idealnej spoiny. Jego fundamentalna rola polega na ochronie jeziorka spawalniczego przed szkodliwym działaniem czynników zewnętrznych, takich jak tlen, azot i wilgoć zawarte w powietrzu. Dzięki temu unikamy utleniania i zanieczyszczeń, co bezpośrednio przekłada się na wytrzymałość połączenia. Ponadto, gaz osłonowy stabilizuje łuk spawalniczy, zapewniając równomierne topienie materiału i tworzenie jednolitej struktury spoiny. Działa on również jak chłodziwo, minimalizując ryzyko przegrzania i deformacji spawanych elementów. Warto pamiętać, że różne gazy osłonowe oferują różne charakterystyki wnikania spoiny – zarówno pod względem głębokości, jak i szerokości – co ma bezpośredni wpływ na wytrzymałość złącza. Co więcej, właściwości użytego gazu determinują cechy mechaniczne spoiny, w tym jej odporność na rozciąganie, twardość i odporność na korozję. Wywierają one również wpływ na estetykę gotowej spoiny, kształtując jej kolor i zapewniając gładkie wykończenie.
Jak działa metoda MIG i jakie gazy są do niej stosowane?
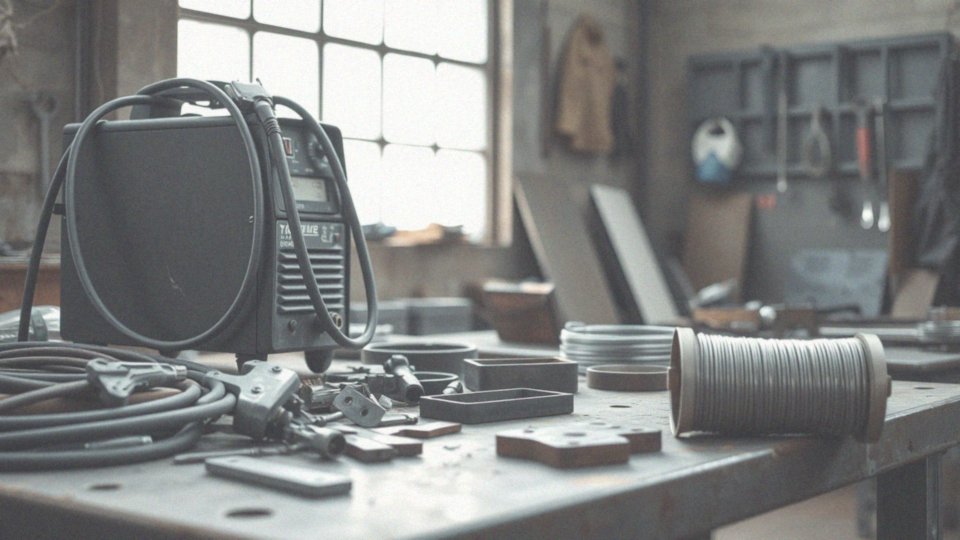
Metoda MIG opiera się na wykorzystaniu gazów obojętnych, które nie wchodzą w reakcje chemiczne ze spawanym materiałem. Ich głównym zadaniem jest stworzenie bariery ochronnej dla spoiny, izolując ją od szkodliwego wpływu atmosfery. Do najpopularniejszych gazów osłonowych zaliczamy argon (Ar) i hel (He).
Argon cieszy się dużą popularnością ze względu na swoją dostępność i szerokie zastosowanie. Gwarantuje on stabilny łuk spawalniczy, minimalizuje powstawanie odprysków i sprawdza się przy łączeniu różnorodnych metali, takich jak aluminium, stal nierdzewna i metale nieżelazne. Hel, choć droższy od argonu, generuje wyższą temperaturę łuku, co przekłada się na głębszą penetrację spoiny – szczególnie istotne przy obróbce grubszych elementów. Stosuje się go głównie do spawania aluminium i jego stopów, zwłaszcza tych o znacznej grubości. Często wykorzystuje się również mieszanki argonu z helem, aby precyzyjnie dostosować właściwości spoiny do specyficznych wymagań danego projektu. Ostateczny wybór gazu zależy więc od rodzaju spawanego metalu, jego grubości oraz oczekiwanej jakości połączenia. Niezwykle istotne jest również zapewnienie odpowiedniego przepływu gazu osłonowego, aby skutecznie chronić spoinę przed zanieczyszczeniami i zagwarantować jej trwałość.
Jak działa metoda MAG i jakie gazy są do niej stosowane?
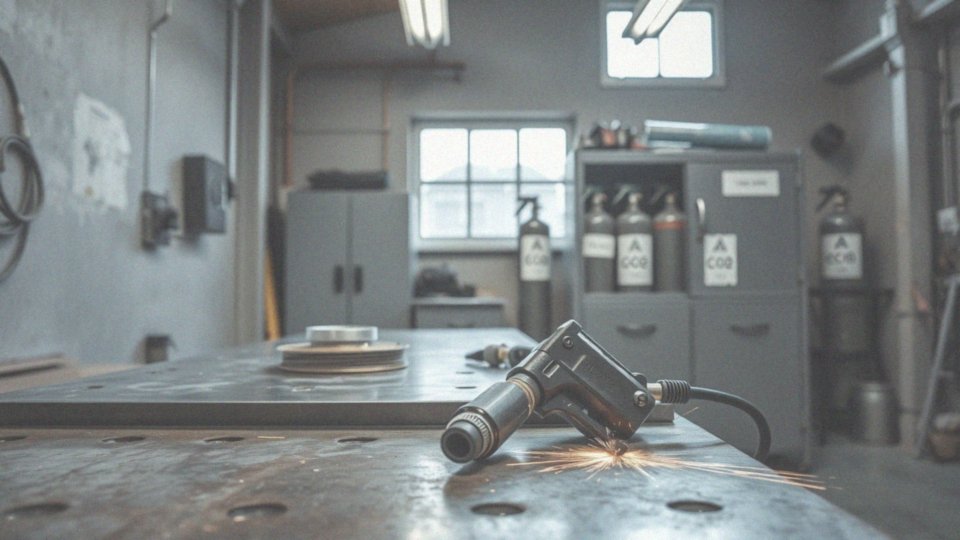
Metoda MAG to popularna w przemyśle technika spawania łukowego z użyciem topliwej elektrody w osłonie gazów aktywnych, opierająca się na gazach wchodzących w reakcję ze spawanym metalem. Najczęściej stosuje się dwutlenek węgla (CO2) ze względu na jego ekonomiczność, co czyni go idealnym wyborem do spawania stali węglowej i niskostopowej. Chociaż CO2 generuje twardszy łuk spawalniczy, bywa on mniej stabilny w porównaniu z łukami powstałymi przy użyciu innych gazów. Alternatywą są mieszanki argonu z dwutlenkiem węgla (Ar/CO2), które gwarantują większą stabilność łuku i lepsze właściwości spawalnicze. Z tego powodu są one powszechnie wykorzystywane przy łączeniu konstrukcji stalowych. Skład mieszanki gazowej jest precyzyjnie dobierany, aby sprostać specyficznym wymaganiom danego procesu i rodzaju spawanego materiału, co ma zasadnicze znaczenie dla osiągnięcia optymalnych efektów spawania.
Jak dobór gazu zależy od spawanego materiału?
Dobór właściwego gazu osłonowego to kluczowa sprawa, ponieważ ma on ogromny wpływ na jakość i cechy spoiny. Decyzja o tym, jaki gaz zastosować, zależy przede wszystkim od spawanego materiału. Przykładowo:
- podczas spawania aluminium najczęściej używa się argonu, który skutecznie zabezpiecza przed utlenianiem i zapewnia stabilny łuk spawalniczy,
- do łączenia stali węglowej i niskostopowej powszechnie wykorzystuje się mieszanki argonu z dwutlenkiem węgla (Ar/CO2), ich odpowiednie proporcje precyzyjnie dostosowuje się do konkretnych wymagań danego procesu,
- w przypadku stali nierdzewnej, często stosuje się osłonę argonową z domieszką tlenu lub dwutlenku węgla, co pozwala uzyskać optymalne parametry mechaniczne spoiny, a także wpływa na jej estetyczny wygląd.
Niestety, nieodpowiedni wybór gazu osłonowego może skutkować poważnymi problemami, prowadząc do wystąpienia wad spawalniczych i osłabienia całego złącza.
Jaki gaz do spawania stali węglowej i niskostopowej?
Dwutlenek węgla (CO2) stanowi ekonomiczne rozwiązanie w spawalnictwie, ale generuje łuk spawalniczy o zwiększonej twardości, co potencjalnie wpływa na jego stabilność. Alternatywą są mieszanki argonu i CO2 (Ar/CO2), które zapewniają łuk bardziej stabilny. Co więcej, wykorzystanie tych mieszanek minimalizuje powstawanie odprysków i podnosi jakość uzyskiwanych spoin. Metoda MAG bazuje na gazach aktywnych, a kluczową rolę odgrywa tu reakcja CO2 ze spawanym metalem. To oddziaływanie bezpośrednio determinuje przebieg całego procesu spawalniczego, podkreślając znaczenie właściwości użytego gazu.
Jaki gaz do spawania stali nierdzewnej?
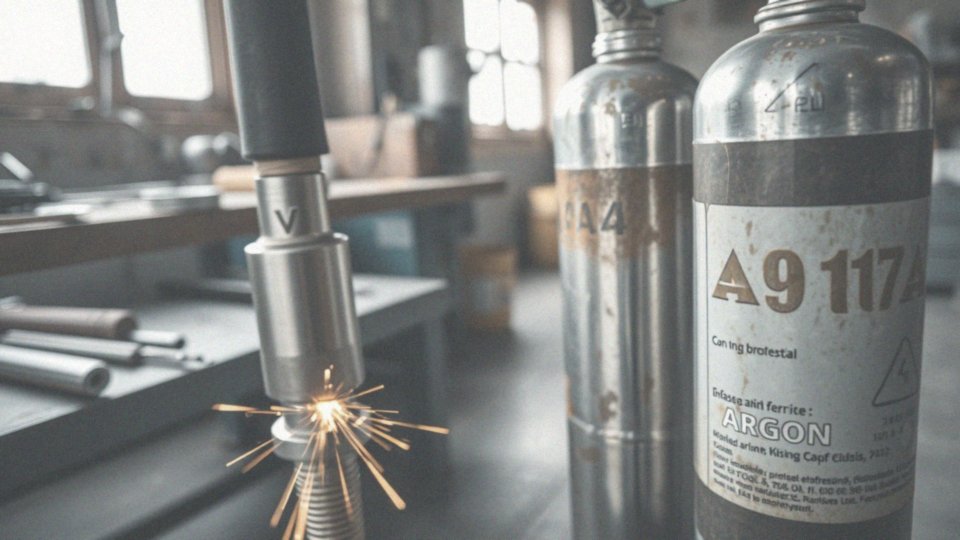
Do spawania stali nierdzewnej najczęściej wykorzystuje się argon (Ar), choć niekiedy spotyka się również mieszanki argonu z niewielką domieszką tlenu (O2) lub dwutlenku węgla (CO2). Argon zapewnia skuteczną ochronę spoiny przed utlenianiem, co bezpośrednio przekłada się na jej czystość i jakość. Z kolei dodatek tlenu lub dwutlenku węgla potrafi znacząco poprawić stabilność łuku elektrycznego, co ułatwia proces spawania.
Należy jednak zachować ostrożność przy wyborze mieszanki gazów, ponieważ wspomniane dodatki nie powinny negatywnie wpływać na odporność spoiny na korozję. Ostatecznie, rodzaj użytego gazu ma fundamentalne znaczenie dla jakości i parametrów technicznych spoiny, w tym jej odporności na korozję i stabilności łuku spawalniczego. W metodzie MIG, ze względu na specyfikę tego procesu, preferowane są gazy obojętne, takie jak właśnie argon.
Jaki gaz do spawania aluminium i jego stopów?
Do spawania aluminium i jego stopów, argon to gaz, który króluje. Zapewnia on skuteczną ochronę przed utlenianiem, co ma kluczowe znaczenie dla trwałości i jakości tworzonej spoiny. Argon stabilizuje łuk spawalniczy i chroni przed zanieczyszczeniami. Alternatywą, szczególnie przy obróbce grubszych elementów, jest hel lub mieszanki argonu z helem. Hel, podnosząc temperaturę łuku, sprzyja lepszemu rozpływowi ciepła i zwiększa głębokość wnikania spoiny. Odpowiedni dobór mieszanki zależy od grubości spawanego materiału i oczekiwanej jakości połączenia. Użycie właściwego gazu osłonowego, takiego jak argon czy hel, wyraźnie wpływa na wygląd jeziorka spawalniczego, minimalizując ryzyko porowatości i innych defektów. W metodzie MIG (Metal Inert Gas), właściwy wybór gazu jest absolutnie niezbędny do uzyskania trwałego i estetycznego połączenia aluminium. Bez odpowiedniego gazu osłonowego trudno o wysokiej jakości spaw.
Jakie gazy są potrzebne do spawania metali nieżelaznych?
Do spawania metali nieżelaznych powszechnie wykorzystuje się argon (Ar), pełniący funkcję gazu osłonowego, który efektywnie zabezpiecza spoinę przed niepożądanym utlenianiem. Jednakże, przy obróbce grubszych elementów z aluminium, magnezu, tytanu lub cyrkonu, zaleca się rozważenie użycia helu lub mieszanki argonu z helem. Takie rozwiązanie znacząco poprawia właściwości spawalnicze, co ma kluczowe znaczenie dla jakości połączenia. Ostateczna decyzja dotycząca wyboru gazu zależy od specyfiki danego projektu, przede wszystkim od rodzaju i grubości spawanego metalu oraz oczekiwanych parametrów wytrzymałościowych i wizualnych spoiny. Właściwy dobór gazu osłonowego jest gwarancją uzyskania trwałego i estetycznego połączenia spawalniczego.
Jakie zalety ma mieszanka argonu i dwutlenku węgla (Ar/CO2)?
Mieszanki Ar/CO2 cieszą się dużym uznaniem podczas spawania stali węglowych i niskostopowych, ponieważ umiejętnie łączą w sobie zalety obu gazów. Argon, stanowiący jeden ze składników tej mieszanki, zapewnia:
- skuteczną ochronę spoiny,
- stabilizację łuku spawalniczego, co znacząco redukuje prawdopodobieństwo wystąpienia defektów,
- zapobieganie utlenianiu jeziorka spawalniczego.
Z kolei dwutlenek węgla, drugi kluczowy składnik, optymalizuje wtopienie i zwilżanie spoiny, przekładając się na jej większą wytrzymałość i estetyczny wygląd. Warto pamiętać, że precyzyjny dobór proporcji mieszanki gazów powinien być podyktowany konkretnymi wymaganiami i potrzebami danego procesu spawalniczego.
Jakie są błędy podczas spawania związane z doborem gazu?
Kluczem do uzyskania wysokiej jakości spoiny jest odpowiedni dobór gazu osłonowego. Niestety, pomyłka w tej kwestii może prowadzić do poważnych problemów. Konsekwencje niewłaściwego wyboru to między innymi:
- porowatość,
- niestabilny łuk spawalniczy,
- nadmierne iskrzenie i odpryski,
- utlenianie spoiny.
Użycie nieodpowiedniego gazu w stosunku do spawanego materiału drastycznie obniża wytrzymałość złącza. Przykładowo, spawanie aluminium w atmosferze dwutlenku węgla (CO2) doprowadzi do utlenienia spoiny, co negatywnie wpłynie na jej właściwości mechaniczne i sprawi, że stanie się ona wadliwa. Należy również pamiętać, że zarówno niedostateczny, jak i nadmierny przepływ gazu osłonowego szkodzi jakości spoiny. Zbyt mała dawka gazu nie zapewni jej należytej ochrony przed wpływem atmosfery, natomiast zbyt duża może spowodować turbulencje. Te z kolei zasysają powietrze do obszaru spawania, co jest wysoce niepożądane. Porowatość spoiny jest problemem, który wynika z wielu przyczyn. Może być ona skutkiem zanieczyszczeń w gazie osłonowym, nieprawidłowego składu mieszanki gazowej lub właśnie niewystarczającego przepływu gazu. Zatem, aby uniknąć problemów, przed przystąpieniem do spawania, należy zwrócić szczególną uwagę na właściwy dobór i parametry gazu osłonowego.